An edited version of this article appeared in the November / December 2011 issue of Canadian Biomass magazine. www.canadianbiomassmagazine.ca
Paul Janzé, Advanced Biomass Consulting Inc.
INTRODUCTION
This article has been the most popular and has received the most attention since I wrote it in 2011. I’ve done a couple of rock removal studies since then and decided the article needed updating with new information.
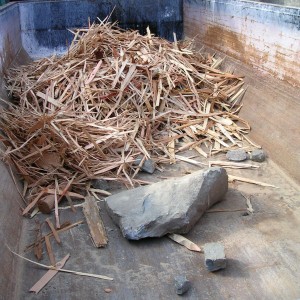
The upsurge of interest in biomass-fired power plants in the past few years is accompanied by a corresponding increase of interest in methods for removing non-combustible, non-organics such as rocks, stones, sand and grit from woody biomass. Rock contaminated woody biomass has long been a problem, and many ways have been attempted in trying to deal with it. The methods are varied, usually depending upon the end-use to which the biomass is being put. There are some specific methods that are very successful; others more a measure of how best to accommodate the problem.
Following is a brief description of the problems, solutions and accommodations that various biomass processing industries utilize when dealing with rocks and other non-organic contaminants in their woody biomass.
Sawmills / Panelboard Plants
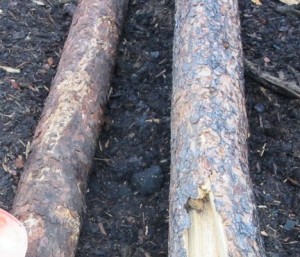
Primary log breakdown facilities, such as sawmills or pulpmill woodrooms, usually remove the bark before processing. Doing so, also removes dirt and stones that have become embedded in the bark during the logging process or while being transported or stored on unpaved areas. Additionally, large rocks can be picked-up by mobile equipment when handling logs and can be dropped onto the log infeed deck, where they get carried along until they fall through openings into the waste conveyors below. The dirt and stones become concentrated in the waste stream, which is often utilized as fuel in biomass-fired energy systems.
In northern climates, other facilities such as panelboard plants utilize log ponds to thaw out or condition (soften) the logs prior to debarking, peeling, chipping or stranding. Much of the embedded dirt and stones falls off the logs in the ponds and the rest is removed during debarking.
Wood Pellet Plants
The standard for domestic wood pellets is <1% of ash, which is quite low; so the wood supply to
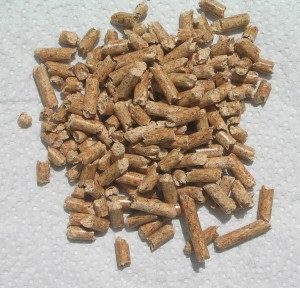
wood pellet plants must be contaminant free. Historically, the furnish for wood pellet plants has been clean, residual sawdust, wood chips or shavings from sawmills and planermills; therefore, rock or sand contamination has not been much of an issue.
However, in the past few years there has been a huge increase in the demand for wood pellets, primarily for the subsidized, domestic European market. North America is the primary source for wood pellets, although other regions are entering the pellet supply chain.
Due to the economic crash in 2008 – 2009, there was a decline in housing starts in the USA that is only now starting to recover. Fewer housing starts meant a decreased requirement for lumber and panelboard resulting in fewer residuals being produced. Concurrently, the global demand for wood pellets increased to the point where the amount of available residuals is insufficient to meet the fibre demand for pellets. These factors have resulted in a shortage of clean furnish for the manufacture of wood pellets. Consequently, pellet producers are utilizing other sources of wood fibre including standing dead wood or other non-merchantable timber with the result being that the fibre supply is often contaminated with dirt, sand and rocks.
In addition to the requirement for low-ash pellets, pelletizers are susceptible to damage and rapid wear, so rock contamination has become a big issue and solutions are being sought for eliminating rocks from the chip supply.
Pulp Mills
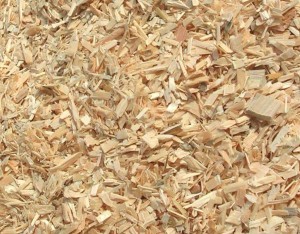
Pulp mills that utilize the Kraft pulping process have found that chips of a uniform length and thickness produce a better quality of pulp. Knots and overthick wood chunks do not `cook’ as quickly in the digesters and recirculate many times through the system taking up valuable production space. Pin chips, long toothpick shaped particles, tend to plug screens, thereby reducing production. And small particles or fines, have been found to require excess amounts of chemical to process through the recovery boilers. Consequently, pulp mills have developed sophisticated multi-stage screening systems to remove gross over-sized pieces of wood, reprocess overthick pieces, regulate the amount of pins being utilized and remove the fines.
One side-effect of the screening system has been the removal of some of the non-organic materials. Rocks larger than the primary screen openings are separated out of the main chip flow along with the overthick chips, which before being reprocessed are first passed through an air density separator (ADS) to remove the rocks which can damage the chip slicers / conditioners. Chip fines passing through the tertiary screens are also removed from the main chip flow to the digester. Sand and grit is coincidentally removed with the fines. These rejected fines are often used as fuel for biomass-fired energy systems.
Refer to the article titled “Benefits of Chip Thickness Screening”, included elsewhere on this website. http://www.advancedbiomass.com/2016/02/the-benefits-of-chip-thickness-screening/
Thermo-mechanical pulp (TMP) mills utilize mechanical refiners to reduce the wood chips to basic wood fibres. The close tolerance refiners cannot tolerate non-organics; so wood chips are first washed to remove stones and grit.
Biomass-fired Boilers
Rocks that are contained in the wastewood stream will be conveyed to the wastewood `hog’ (grinder) and can be smashed by the rotor hammers. Doing so can cause, at the least, rapid component wear, and at the worst, damage to the rotor and grates. The contaminated, processed hog fuel is often used as fuel for biomass-fired energy systems.
Mass-burn biomass boilers are fairly tolerant of non-combustible non-organics, most of which are removed with the left over bottom ash. However, large rocks can cause problems in the fuel handling system and downstream operating problems in the ash handling systems. Small stones and pebbles can get caught between the combustor’s bottom grate bars causing them to jam-up and break,. At the other end of the ash size scale, very fine particles of sand being carried by the flue gases can seriously abrade the pressure tubes in the boiler.
Bubbling fluidized bed (BFB) boilers are designed to utilize sand as an efficient medium for transferring heat to the biomass fuel and are especially effective with biomass fuels with high moisture contents. Combustion air is blown through the sand bed and the fluidized sand is mixed with the burning fuel which is quickly dried, heated and combusted. Rocks entering with the biomass fuel do not fluidize and accumulate in the bottom of the boiler; so a fraction of the fluidizing sand containing the rocks is continuously removed from the boiler bottom. Some plants screen the rejected sand to remove the rocks, clinker and fines; others simply send it to landfill. Sand entering the boiler with the biomass makes up some of the sand loss, but other new sand must be purchased to replenish the lost sand.
Generally, keeping rocks out of the biomass fuel supply reduces boiler operating downtime and lowers operating costs, particularly so for power plants, which have strict penalties for unplanned outages off the grid. The rock contamination problem is somewhat less problematic for industries that have their own cogeneration (Cogen) or combined heat and power (CHP) plants and utilize the heat and steam internally.
CONTAMINATION WITH NON-ORGANICS
Contamination can consist of varying amounts of sand, dirt, grit, and small and large stones; and
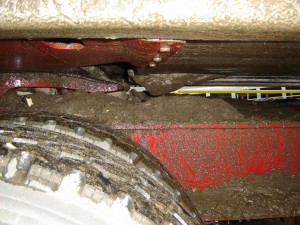
generally occurs as a result of poor handling practices, including:
- Dragging felled wood along the ground where dirt and rocks can become embedded in the bark.
- Dirt, grit and stones can build-up on transport trucks and if not properly cleaned-off, find their way into the biomass stream when the trucks are emptied at the plant.
- Storing woody biomass on unpaved ground. Even providing for a sacrificial layer of biomass, rocks will work their way up from the underlying soil and be picked up by mobile equipment moving the biomass to the plant.
- Picking up grit and stones when reclaiming roadside logging debris (RLD) stored on unpaved pads.
- Not taking the requisite care with primary plant residuals; i.e. – allowing clean sawdust or chips to be mixed with `dirty’ bark.
The best method of minimizing rock contamination is to prevent the non-organics from entering the
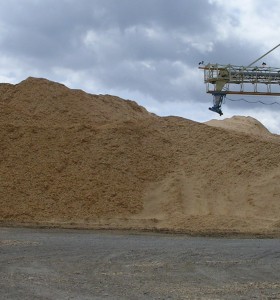
biomass flow in the first place. One pulp mill found that rocks were migrating from the unpaved chip storage yard into the chip supply, so paved the storage pad. Once the area was paved, the rock contamination problem went away. Another mill found that removing the sand, snow and small stones that fell off trucks onto the truck dumper before they could get into the chip stream solved their contamination problem.
As it is not always possible to prevent rocks from entering the biomass flow, some form of rock removal is sometimes necessary. However, trying to remove 100% of the non-organics from 100% of the material stream is costly. Before selecting a rock removal system, first determine which size range of rock particle is causing the trouble and design a system to remove it.
ROCK REMOVAL METHODS
Effectively removing rocks from biomass requires a lot of equipment that is costly to operate. There are a few methods of rock removal, including:
- Water Bath Rock Separator
Most woody biomass is lighter than water and floats; most sand and rocks are heavier and sink,
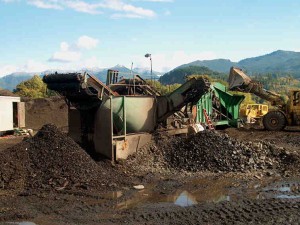
which makes the water bath effective for removing heavy non-organics. So, if excess moisture in the biomass is not a process issue, a water bath can be used for removing sand, grit and rocks from ground-up biomass. The lighter, buoyant biomass floats on top of the water and can be floated off while the heavy non-organics sink to the bottom. Water baths are more suitable for separating large particles where the surface-to-mass ratio is quite low and the consequent surface water pick-up is low, as contrasted to small particles with a high surface-to-mass ratio.
However, the water bath has serious disadvantages, including:
- Moisture pick-up in the biomass, which if used as fuel in a biomass boiler causes problems in the combustor and decreases output.
- If you operate in a very cold climate, the wet biomass can freeze into lumps.
- The cleaning water quickly becomes contaminated and must be continually refreshed. Treating the wastewater can be costly, unless the facility already has a plant with a large wastewater treatment system.
- Air Knives
The simplest rock removal system utilizes a wide high-speed belt conveyor that throws the material
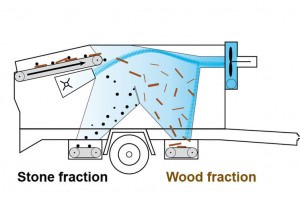
in a thin stream across an air gap. The trajectory is just short enough that the material won’t reach the downstream conveyor without assistance, which is provided in the form of an air stream from an air knife. The air knife is an air chamber that is mounted underneath the conveyor head pulley and has a narrow slit the full-length through which low pressure, high velocity air is blown underneath the falling material. The air jet catches the lighter material and blows it across the gap onto the downstream conveyor. Heavier particles fall through the air stream into the gap and land on a rejects conveyor that transports the `heavies’ away from the main product stream.
As with all systems that utilize air, air knives work on a narrow density band, so it is best to use them on material previously classified by size.
Air knives pressurize the conveyor enclosure and without dust control, fugitive dusting is an issue.
- Air density Separation (ADS)
There are many systems available that utilize air streams to separate particles by size and density.
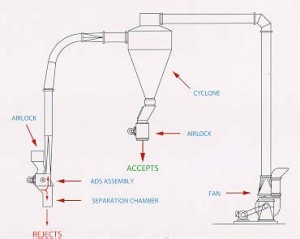
Typically the lighter particles are carried in the air stream and the heavier particles fall-out of the air stream. These systems work well, but their big disadvantage is that they are only effective over a narrow density band where the particles are similar in size. This necessitates separating the material into different sized particle streams before treating each stream over an air density separation (ADS) system custom designed for that particle size. Dust control is required to meet emission standards.
High capacity air density separation systems utilize high volume, low pressure air to separate heavies from lights. A fan produces a negative pressure in a cyclone, which draws air up through a pipe connected to a separation chamber. A rotary feeder meters the material into the up-flowing airstream inside the separation chamber. The `heavies’ fall out the bottom of the chamber and the `lights’ are carried up the air pipe into the cyclone, which separates the material from the air stream. A rotary airlock discharges the collected `light’ material from the bottom of the cyclone. The cleaned material is conveyed away for further processing.
ADS systems are custom designed for specific particle sizes and material densities, and can be adjusted during operation for different flows and separation classifications. ADS systems are used in pulpmill chip thickness screening systems for removing heavies such as rocks and knots from the chip flow prior to a chip slicer / conditioner.
Air density separation (ADS) systems are effective at rock removal, but also have disadvantages, including:
- A large piece of wood can weigh more than a small pebble, so ADS systems effectively work only over a small range of densities, where the particles are similar in size.
- Large volumes of air are required, resulting in large fans and motors.
- Effective air clean-up systems are required that will meet emission standards.
- ADS rock removal systems usually require a considerable amount of equipment, require large supporting structures, have a big footprint and are costly to construct and operate.
- Screening for Size and ADS
If only one particular size of rock is causing problems, screen-out that size of particle and discard it. However, you will also be discarding similar sized particles of biomass, which may or may not be acceptable.
Generally, I have found that a combination of screening for size and air density separation is the best dry method of removing rock particles from biomass. First screen the entire product flow into different size classifications, one or more of which will contain the offending rock particle size. Then process the selected contaminated stream through an appropriately designed air density separator to separate the biomass from the heavier non-organics.
In most cases it is fairly easy and not too costly to retrofit a rock removal system into industrial processes that already utilize multi-levels of size screening, as many of the required components are already in place.
One example is a pulp mill that discovered that rocks 1/4” – 3/8” were causing substantial wear to
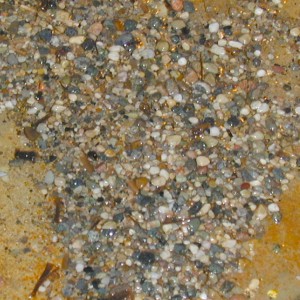
the pulp screens. This mill already had (3) levels of chip size screening in place for other process purposes. It was found that most rocks larger than 3/8” were being removed by the primary screen and overthick ADS system; and sand and grit smaller than 1/8” were being removed by the tertiary screen. But rocks between 1/8” and 3/8” were staying in the chip flow to the pulp mill digester. It was also found that these sizes of rocks were concentrated in the chip flow from the secondary to tertiary chip screens; consequently, it was recommended that this contaminated stream be diverted off-line to an ADS system where the rocks could be removed.
- Fluidization and Vibration
Some rock removal systems utilize a combination of fluidization and vibration to separate lights and heavies. The equipment consists of an inclined, perforated, vibrating fluidization plate. Air is pumped into a chamber underneath the plate and escapes upwards through the perforations, the intent being to fluidize the material on top. Material is fed onto the center of the plate; the fluidized light material floats downwards off the sloped plate and the heavies are vibrated off the upper end of the plate.
Such systems that utilize fluidization and vibration work best with low flows of uniformly sized and shaped material. To our knowledge such a system has not been utilized on wastewood.
- Screening, Vibration, Fluidization and Air Knives
This combination of processes is best demonstrated by the vibrating destoner, which is specifically
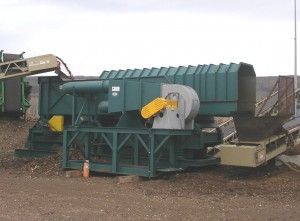
designed for removing rocks from biomass and comes in several configurations. The basic machine is a vibrating conveyor with one or more integral air knives operating in a similar fashion to the air knife described above.
A perforated plate is located in the bottom of the vibrating pan just before the air-knife, which is located underneath an opening in the bottom of the vibrating pan. Low pressure air is blown into a chamber below the perforated plate and escapes upward through the perforations, the intent being to loosen and fluidize the light material just before it falls over the edge of the air-knife opening.
Air is blown into the air knife which has a narrow slit the full-length. High velocity air from the air knife blows the light material across the gap onto the downstream vibrating pan. Heavies fall through the gap into a chute and out the side of the vibrating conveyor. Multiple air-knives can be installed in a destoner to provide different classifications.
The destoner is also available with a vibrating screen section for providing a secondary size classification. Material smaller than the screen opening falls through the screen onto a second vibrating deck and is either discharged from the machine or carried to a second destoner air knife.
Destoners work best where the particle size is fairly uniform and the flow is metered onto the destoner presenting an even depth of burden (DOB) to the air knife.
The inside of the destoner is under a positive pressure from the fluidizing air / air knife fan(s). To minimize fugitive dusting, it is recommended that the air be recirculated from the destoner hood back to the fan inlet, first passing through a high efficiency cyclone to clean the air. Additionally, the destoner hood should be connected to a dust extractor / collector to remove some of the air and keep the destoner under a negative pressure, thereby reducing fugitive dusting.
Refer to the attached typical destoner process flow diagram.Typical Destoner PFD-001
Dust Control
All biomass handling and processing systems produce dust, which if not handled properly can cause health, safety and environmental problems. Equipment that relies on air being injected inside it becomes pressurized and as the air escapes from the enclosure, it takes the airborne dust with it.
Airborne dry dust is flammable and highly explosive in the right concentrations. Having an effective dust control system in place to control fugitive dusting is paramount when handling dry biomass. For more information, refer to the article titled “Biomass Dust Fire and Explosion Control”, located elsewhere on this website. http://www.advancedbiomass.com/2013/04/biomass-dust-fire-and-explosion-control/
ROCK REMOVAL SYSTEM FOR BIOMASS FUEL
In my experience, the simplest and most effective rock removal system for biomass would include
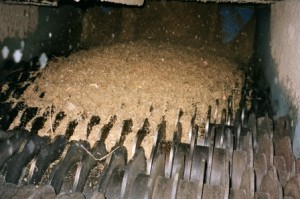
the following equipment:
- A heavy duty disc scalping screen for removing large rocks, lumps of frozen biomass, and large chunks of wood
- A robust trommel screen with (1) or (2) different screen sizes depending upon the rock size to be removed.
- The grit-laden fines would fall out of the first screen section.
- An intermediate particle size would fall out the second screen section (if installed)
- The very large pieces of material would pass out the end of the trommel screen
Gross-Overs
- One or both of the larger sized streams could be passed over a vibrating destoner conveyor equipped with one or two air knives. Heavy particles would fall out the opening at the lip of the air knife; and lighter particles would be blown over the gap. Cleaned material is discharged out of the end of the destoner.
- If required, the grit-laden fines could be cleaned on a dedicated ADS system.
- If there was an excessive amount of gross oversized material, it could be further processed on or off-site in a grinder / hog.
- A dust control system would be required.
Combination Vibrating Grizzly and Trommel Screen
Biomass Screen Vendors
There are several types and makes of screens that are used for processing biomass.
- Scalping screens – the heavy duty disc type of screen is made by: Rader (Terrasource), Acrowood Corp., West Salem Machinery, and many others.
- Trommel screen – good for most biomass fuel, made by: PowerScreen, McCloskey, West Salem Machinery, Tuffman and many others.
Tuffman – Typical 3-Classification Trommel Screen - Gyratory screens – very good for chips, sawdust and shavings, made by: BM&M, Acrowood, Bruks, and others.
- Thickness screens – specific to pulp mills made by: Rader (Terrasource), Acrowood Corp.
- `Flip-Flow’ screens – perforated plastic mat screens, made by: Hein-Lehman, Rader (Terrasource), Action Vibratory Equipment.
Air Density Separation Equipment Vendors
Air Density Separation equipment, includes:
- Vibratory destoners with air knives made by: General Kinematics, Action Vibratory Equipment.
- ADS systems made by: Rader (Terrasource), Acrowood Corp.
- Equipment for sand/grit removal from small particles, made by: Rader (Terrasource), Clarke’s Industries.
For more information regarding biomass screening, refer to the article titled “Screens for Woody Biomass”, elsewhere on this website. http://www.advancedbiomass.com/2013/11/screens-for-woody-biomass/
Copywrite © 2016
ABOUT THE AUTHOR
Paul Janzé has more than 30 years experience in engineering design, project management, equipment manufacturing and maintenance, primarily in the forest products and energy industries. His industrial material handling experience includes: biomass handling and processing including forest residuals, logs, lumber, chips, pellets, woodwaste, corn stover, straw and poultry litter, deinked pulp, sludge and biosolids; municipal solid waste (MSW); limestone, coal, ash handling and petroleum coke.
He has a keen interest in technologies which recover and utilize waste materials and convert them into products such as wood pellets. Paul’s specialties are fibre flow analysis and mass balances, process optimization and designing novel solutions to complex processing and handling problems
Paul can be reached at: Advanced Biomass Consulting Inc., tel: 1-604-505-5857, email: pjanze@telus.net
interrestted in a water bath for bark plant. kerry.newton8@gmail.com
Hi Paul
Just found your blog today; I have been a clearing and grubbing contractor in the Lower Mainland for 25 years; we use a Morbark 8535 Forwarder/Dump Box conversion to haul clearing biomass to a roadside grinder then truck grindings to North Langley for barge loading.
I am looking to expand our operations into the Interior to process beetle kill biomass. Do you know who to contact for more information on what work is available? Thanks
Hi Brent,
Thanks for visiting my website. I would try contacting the major forest products companies, such as West Fraser Timber in Quesnel; Canfor in Prince George.
Paul
Hi,
My name is Chris Wright and I currently work at a paper mill in Atlantic Canada who has recently installed a Wellons Biomass Boiler. Right now they are having server clinkering problem within their furnace cells (4 altogether) and cannot figure out how to counteract the issue. They have tried fuel variations to adjust furnace temperatures, air quantities, everything. Could you possible e-mail me a little background information on how these clinkers would actually come about? And what sort of conditions would be ideal for a boiler burning bark (often times clean and dry, but occasionally we get a few damp more “dirty” loads with some soil/silt mixed in). I would appreciate any information. My e-mail is cwright16@hotmail.com
Thanks in advance,
Chris
Hi Chris,
Thanks for visiting my website.
I believe my colleague, Rob Stewart, spoke with you and provided some guidance. Did you find his input useful? Is there anything else that we might be able to help you with.
Paul
Hi Paul! Curious: Have you ever dealt with salt hog/wood waste? Is there any method to clean the salt out effectively without using a whole bunch of water to do so?
Thanks Paul, great site!
Hi Jean,
Thank you for visiting my website.
Yes, salt in woodwaste / hog fuel can be a real problem, particularly here on the west coast (BC) where either the logs have been transported by water in log booms or hog fuel barges have been transported long distances in open water. The salt saturated bark can cause problems with hog fuel boilers and pollution control equipment. Unfortunately I know of no way of removing the salt, short of washing it prior to usage; and if you are using the hog fuel for fuel, you would then have to dry it. I know that some plants have successfully used wet electrostatic precipitators to clean the salt from boiler exhaust gases after combustion.
What are your circumstances that prompted the query?
Paul
Hi,
we procured chopped bio mass of soya bean, cotten, maize etc. to use as boiler fuel. Most of the time we found defferent size of rock, soil lumps etc. in the same bio mass which creat lot of problems in our fludised bed combustion firing system in boiler.
kindly suggest some solution.
Thanks n wid regards
kuldeep (India)
We are planning to remove rocks and tramp metals from the overs stream from a scalping screen (>3″).
A water bath seems appropriate as the volume is small (< 7 tph) and freezing is not an issue. Floating wood and plastics would be shredded to <=1". Your thoughts on the application. Do you have a recommendation for a water bath supplier?
Arnie
Hi Arnie,
Thank you for visiting my website. What is the name of your company and where are you located?
Removing rocks and metal from oversized scalping screen rejects can be done with a water bath, if freezing is not a problem. And, I assume that the use you have planned for the cleaned oversized material is not as a fuel, as I think that you would not want to be wetting it.
Water bath complexity can range from a simple water-filled tank that is manually cleaned, to one which has conveyors for removing the `heavies’ and `floaters’.
7 tph of material >3” is not a large amount of material, but it’s enough that I don’t imagine you want a person in constant attendance or to manually clean the tank. I would assume that you would want a conveyor to remove the heavies from the bottom of the tank and likely a conveyor to remove the `floaters’ from the top of the water.
Water baths are generally custom designed for the specific application. The design depends upon:
– the amount of material to be processed
– the amount of rocks and metals present
– the physical layout of the plant
– the amount of `tending’ labour the client wants to eliminate
– the amount of water available
– the requirement (or not) to clean the water after use
The only commercially available water bath systems I know of are high-volume chip washers in TMP pulpmills, or water baths in log chipper feed systems, which I believe would be too large and much too costly for your application. The least costly solution would be to have a water bath custom designed and fabricated for your particular use.
I would be glad to help you with the specifications and design for a water bath that you could have locally fabricated. My rates are reasonable. Please let me know if you are interested and I will prepare a proposal for your consideration.
Paul Janze
Advanced Biomass Consulting Inc.
pjanze@telus.net
Hello, I would like some advice on bark rock separators. We have a large log yard. I need to take log yard bark and separate the rock and sticks from the good bark. A water separator in our Montana climate I don’t believe would work with the low temperatures. Do you have any ideas? Thanks
Hi Anthony,
Thank you for visiting my website. A waterbath would be effective during the summer, but not work during the winter. So, about the only effective method would be a combination screening / air density separation system similar to that described in my article “Rock Removal from Woody Biomass”. The extent of equipment required depends upon:
– the amount of material to be processed
– the size range of rock and sticks that you want to remove
Would this be a continuous process or do you clean up the yard once a year?
Before I could make any real recommendations, I would need considerable more data, including:
– description of material handled: species, size distribution, moisture content, size to be removed
– description of rock contaminants present: size distribution, size to be removed
– amount of material to be processed; i.e. – tonnes per hour or cubic yards per hour
– continuous process or batch process
If you are interested, I would be pleased to submit a proposal for providing consulting assistance to assess your situation and design a system that would meet your requirements.
I look forward to hearing from you.
Paul Janze
Advanced Biomass Consulting Inc., Langley, BC
604-505-5857
pjanze@telus.net
Dear Paul,
I work for Global energy Pvt. Ltd, a 5MW biomass power plant mainly bagasse being the fuel, Its boiler is of travel grate system (John Thomson),
we find a lot difficulties while feeding bagasse, as many a times stones/pebbles come through bagasse
& same is being fed later which damages the travel grates & damages the same which is very expensive.
Please do the needful
Thanks
Imran M
Hi Imran,
As noted in my article “Rock Removal from Woody Biomass”, it is technically feasible to remove stones and pebbles from biomass. The first step is to determine the size range of the stones that are causing the problem; next, screen the biomass such that you concentrate that size range of stone in one material flow. The last steps are then to process that selected material stream through an air density separator (ADS), sized and custom designed to remove the identified size range of stone and then reintegrate the screened material into the flow to the biomass combustor. It sounds simple, but there are several important design considerations. The material characteristics need to be properly identified, and any potential changes in material noted. The amount of material being processed needs to be identified and accommodated in the equipment design. ADS systems are notoriously dusty, so properly designed dust control systems are required. The dust if dry and in the right concentrations is likely explosive, so care must be taken to consider spark, fire and explosion prevention, detection, and suppression.
Lastly, these systems are costly to install and operate and are oftentimes difficult to justify, particularly if potential maintenance savings are the only benefit. If the current problem leads to equipment being out of service and loss of revenue, or is a safety issue, then you might be able to justify the cost.
Probably, the least costly method is to prevent the stones and rocks from entering the material flow in the first place. You may be able to reduce the amount of rock contamination simply by visiting the raw material source and observing the material handling procedures and instituting better handling procedures.
If you need assistance assessing the problem and evaluating solutions, please let me know and I would be pleased to provide a proposal to do so.
BTW, where are you located.
Paul
We are looking for a machine that can remove rocks, and or any unwanted foreign matter in a bean food processing plant. Sometimes the sacks of beans has rocks or wood. We have efficient metal detection however those technologies do not work for wood and rocks.
If you can help please call me 6023267730
Hello Thomas,
Thank you for visiting my website, http://www.advancedbiomass.com . Removing rocks from beans can be accomplished with a combination of fluidizing air and vibration. You would likely be able to remove large pieces of wood this way too; however, maybe not smaller pieces of wood, similar in size and density to the beans.
I like to know who I am communicating with. What company do you work for and what is your position?
I don’t sell equipment, but would be pleased to work with you to solve your rock / wood contamination problem, by assessing your process flow and making recommendations for the best equipment. My rates are quite reasonable. Let me know if you are interested.
Paul Janze
Advanced Biomass Consulting Inc., Langley, BC
604-505-5857
Hello,
I am a final year chemical engineering project student. I need an equipment for removing stones and sand from cassava roots after harvesting before the roots are used for cassava starch processing. I would be glad if you could offer help.
Hi Paul
Who would be the manufacturer of the water bath separator in the picture? Incidentally, there are manufacturers in Scandinavia that I know, but I have to locate someone in US or Canada, either a manufacturer or anybody renting out such equipment.
Cheers
A.J Numminen
Finland
Hello Mr. Numminen,
Thanks for visiting my website, and I am glad that you found the article interesting.
I see that you work for Saalasti. I am very familiar with your bark presses having worked on projects with Finnex over the years here in BC.
The waterbath separator in the photo was a used one on sale by BioReclaim Inc. in Sheridan, OR.
In my >30 years of experience with wood and biomass engineering, I have designed water baths as part of debarker / chipper systems. So, if you can’t find one `off-the-shelf’ here in North America, I would be pleased to work with you to custom design one to meet your client’s requirements.
Let me know if this is of interest to you, and I will prepare a proposal upon receipt of your RFP.
Advanced Biomass Consulting Inc.
Langley, BC Canada
tel: 1-604-505-5857
pjanze@telus.net
Hi Paul
I contract to a sawmill that supplies hog fuel to the pulp mills to burn but the big problem is there is a lot of contamination from stones.. I have previously built bark screening plants but in your opinion what is the best method. Must admit the air knives seem to be the most effective!
John
Good Afternoom Paul and greeting from Grand Cayman, Cayman Islands
My questions: Iam currently writting a business plan to establish an operatio on island to: 1) generate a mulch product from tropical brush & wood. 2) a compost from yard and geen waste un processed foofd waste resorts & restuarants. 3) screened loam from raw sool excavation and brackish peat to a 3/8″ and 1/2 screening plant (vibratory and trammal) 4) biofuel from storm wood waste from intake product pallet waste and wood demo. I also want to further process tailings from screening operation into the mulch/ biofuel and rocks into sorted particle sizes 3/8,”, 1/2″, 3/4″ and 11/2″ amd over 11/2″ size aggregate crushing larger to tje previous sizes. All raw product is coming into waste syteam currently being landfilled. The plan is to reduce and recycle waste stream. Provide mulch, compost and aggregate which is very expensive to import. Provide topsoil and blended soils for athletic/ golf/landscape/agriculture. At this point preliminary machine selection and viable quotes need to be established. Tub grinders, horizontal grinders, trammal.plants, vibratory screeners, sorters, stacker conveyors and crushing plant. Water is an issue here as all ftesh water is RO made and very expensive. Air knife systems would work better for sorting wpod from rock debris for biofuel and mulch compost grinding. Idont think i want to water bath the materials in brackish/ salt water. Any advice or direction for further info would be helpful. (Originally a Boston Boy)
Good day Paul.
I have an application where I need to remove saturated vegetation from rocks and sand. A water bath is what I am looking at but my saturated vegetation is measured at an sg of 1.1 – 1.2 meaning they do sink, slower than the other rock but it does sink. Have you ever came across this and will a water bath work?
I am currently on a project in Saskatchewan so for the following three weeks before I head back to South Africa.
Regards.
Konrad Myburgh
Hi Paul,
Lots of good info on your website. .problems i have run into in the last 10 yrs or so.
i have an application where i believe a water bath, would work :??
this material is from a shredder working at a Landfill– so its quite contaminated.
this material is screened, to 1in particle size, with about a quarter of it being sand/gravel.
Also material is wet- this is not a problem, as my boiler can burn biomass with up to 40% moisture. but not with the sand and gravel.
would you help me with designing a water bath for my system? or would air separation work better?
thinking around 20-ton hour range.
Thank You.